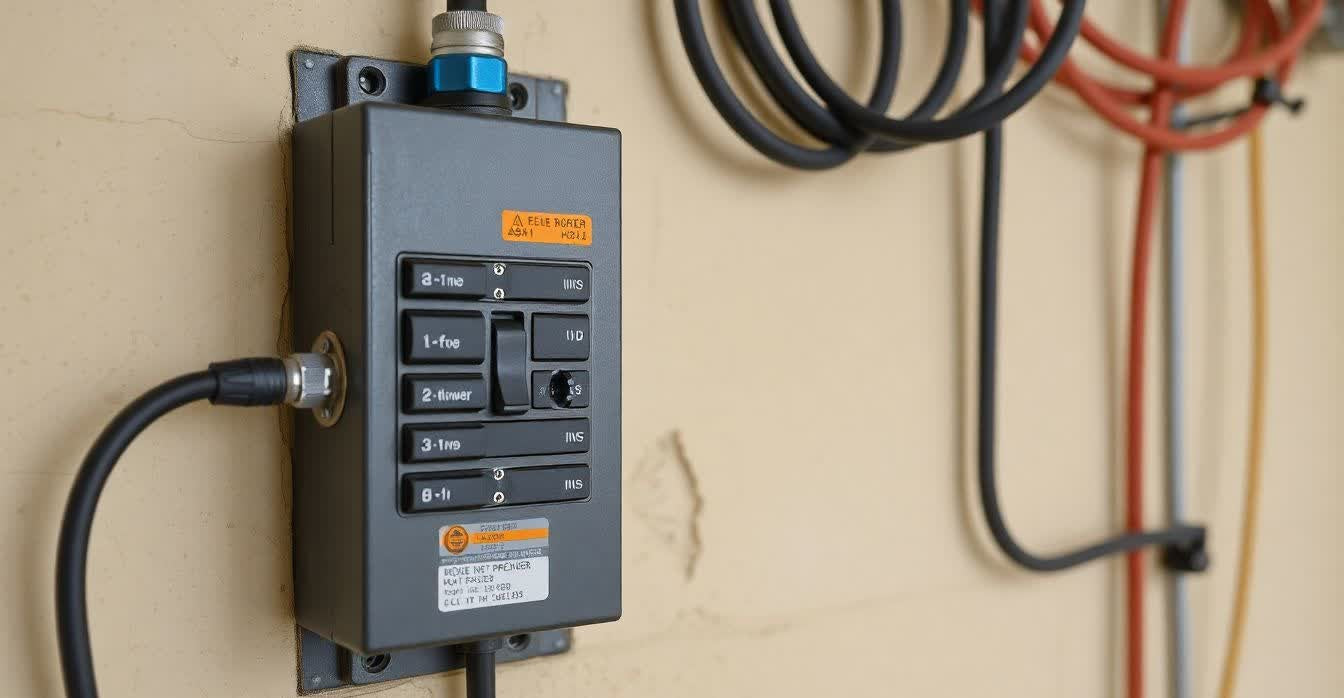
The Importance of Regular Thermographic Inspections for Electrical Panels
Electrical panels are the backbone of any home or business’s electrical system, ensuring power is distributed safely and efficiently. However, over time, wear and tear, loose connections, or overloaded circuits can lead to overheating, which poses significant fire risks. Regular thermographic inspections, also known as infrared (IR) scans, are a proactive way to identify potential issues before they escalate into costly or dangerous problems. Here’s why these inspections are essential for maintaining safe and reliable electrical systems.
1. What Are Thermographic Inspections?
Thermographic inspections use infrared cameras to detect heat patterns and temperature anomalies in electrical panels and components. Excessive heat often indicates problems such as:
- Loose or corroded connections
- Overloaded circuits
- Failing breakers or switches
- Imbalanced loads
By identifying hotspots that are invisible to the naked eye, thermographic inspections provide early warnings of potential failures, allowing for timely repairs.
2. Preventing Electrical Fires
One of the most critical benefits of thermographic inspections is their ability to prevent electrical fires. Overheating components are a leading cause of electrical fires in homes and businesses. For example:
- A loose connection can generate excessive heat due to increased resistance.
- Overloaded circuits may cause wires to overheat, damaging insulation and increasing fire risks.
Thermographic scans pinpoint these issues before they reach dangerous temperatures, enabling electricians to address them promptly and mitigate hazards.
3. Improving System Reliability
Regular inspections ensure that electrical panels operate at optimal performance levels. By identifying and resolving minor issues early, you can avoid unexpected breakdowns and downtime. This is especially important for businesses, where electrical failures can disrupt operations, lead to lost revenue, and damage reputations.
For homeowners, reliable electrical systems mean uninterrupted power for essential appliances, lighting, and HVAC systems, enhancing comfort and convenience.
4. Extending Equipment Lifespan
Heat is one of the primary factors that degrade electrical components. Prolonged exposure to high temperatures can cause breakers, wiring, and other parts to wear out faster than expected. Thermographic inspections help identify and resolve overheating issues, reducing stress on equipment and extending its lifespan. This not only saves money on replacements but also ensures your system remains efficient for years to come.
5. Cost Savings Through Early Detection
Addressing electrical issues early is far more cost-effective than dealing with the aftermath of a failure. For instance:
- Repairing a loose connection costs significantly less than replacing an entire circuit breaker panel damaged by a fire.
- Preventing downtime in a commercial setting avoids losses associated with halted operations.
Thermographic inspections allow you to catch problems in their infancy, minimizing repair costs and avoiding catastrophic failures.
6. Compliance and Insurance Benefits
Many industries require regular thermographic inspections as part of safety compliance standards. Additionally, insurance companies often view these inspections favorably, as they demonstrate a commitment to risk management. In some cases, businesses may even qualify for reduced premiums by implementing routine inspections.
7. Non-Invasive and Efficient Process
Unlike traditional inspection methods, thermographic scans are non-invasive and do not require shutting down the electrical system. This makes them a convenient and efficient way to assess the condition of electrical panels without disrupting daily activities. Trained technicians can complete the inspection quickly and provide detailed reports highlighting areas that need attention.
8. When Should You Schedule Thermographic Inspections?
The frequency of thermographic inspections depends on the type of property and its electrical demands:
- Residential Properties : Every 2–3 years, or sooner if you notice flickering lights, tripped breakers, or unusual odors.
- Commercial Properties : Annually, or more frequently for facilities with high electrical loads, such as manufacturing plants or data centers.
- After Major Renovations : If new equipment or circuits have been added, schedule an inspection to ensure everything is functioning correctly.
Conclusion
Regular thermographic inspections are a vital tool for maintaining the safety, reliability, and efficiency of electrical panels. By detecting overheating and other issues early, these inspections help prevent fires, reduce downtime, and extend the lifespan of equipment. Whether you’re a homeowner or a business owner, investing in thermographic inspections is a proactive step toward safeguarding your property, protecting your loved ones or employees, and ensuring uninterrupted power. Don’t wait for a problem to arise—schedule an inspection today and stay ahead of potential risks.